1 Introduction
This article refers to the address: http://
As global energy and environmental issues continue to emerge, as a major consumer of oil consumption and carbon dioxide emissions, China's car ownership continues to rise, not only brings a crisis to energy, but also the exhaust gas of traditional cars has brought great harm to the environment. The automotive industry needs revolutionary changes. The development of new energy vehicles has become the consensus of all countries in the world. With the advancement of science and technology, electric vehicles, hybrid electric vehicles and fuel cell electric vehicles with energy saving, environmental protection and safety as the ultimate goals. The research and development and application have become the focus of the development of the automotive industry in all countries of the world. China has included it among the seven strategic emerging industries.
Parallel to development and challenges, electric vehicle safety accidents have occurred in recent years, causing concern. As the core component of electric vehicles, automotive lithium battery packs ensure the safe driving environment of electric vehicles and ensure the safety of drivers. The collection and analysis of lithium battery data is undoubtedly for the automotive battery development team and related vehicles. The department provides strong data support for battery pack development and upgrades.
The CAN bus is derived from the automotive industry. Its high anti-interference ability, stable communication, strong compatibility, etc., has long-term and stable application in the automotive industry. CAN networks are used in all automotive networks, such as power control networks and body comfort. And entertainment networks, etc. In order to seamlessly be compatible with the original automotive network control and management system, the communication and management of the battery pack of the new energy electric vehicle has adopted the CAN bus as the first choice. Since the capacity and quantity of the battery pack of an electric car determine the driving performance of the car, the power battery needs to be combined with hundreds of single cells. Usually, the electric passenger car is composed of 40 to 100 battery cells to ensure the basic driving stroke. Guarantee. On the one hand, in order to ensure the consistency of the single cell, improve the overall life of the battery pack, and study the battery and improve its efficiency, it is necessary to collect a large amount of battery data for analysis, and it is necessary to effectively work on the voltage, current, and current of each cell. The power is monitored and collected, and the power conversion rate of the battery is analyzed in parallel with the power parameters of the vehicle speed, engine speed, motor speed, etc., so it is necessary to collect the operating parameters of each unit in the battery pack in large quantities.
On the other hand, different cities in China have proposed data acquisition parameters and requirements for new energy vehicles. In addition to the parameters related to the power battery pack, power battery temperature, battery fault code, motor fault code, GPS information, mileage, etc. In this context, more than 20 sets of parameters are collected. In this context, this paper introduces and provides a new energy vehicle battery data scheme based on CAN bus. The car CAN bus data recorder neoVI FIRE uses large-capacity storage to save all parameters, and offline. The way of recording eliminates the need for manual follow-up work. The host computer configuration software Vehicle Spy3 provides a logical and functional recording solution. Currently, the program has been applied to many new energy vehicle battery research departments.
2. Current status of electric vehicle battery collection
Since electric vehicles are emerging industries, they have not been widely promoted and used due to various reasons. In order to deeply study electric vehicles and enhance the competitiveness of electric vehicles, many automotive research institutes and other institutions will be equipped with different battery data recording devices. There is no uniform standard; different battery data loggers have different acquisition parameters, and the generated log files are different, resulting in poor interoperability and compatibility. Some battery data loggers have different appearances and may not meet the installation requirements of the car, and may not achieve the recording and storage functions of large data volumes.
In this paper, according to the actual demand of electric vehicles for data collection, a multi-channel vehicle data recorder neoVI FIRE is provided. On the one hand, it can record the battery state during the actual operation of the electric vehicle, such as the cell voltage, current, temperature, capacity, and the like. On the other hand, neoVI FIRE's multi-channel function can simultaneously record real vehicle data (DBC parsed) on the car power CAN bus, such as vehicle speed, engine speed, mileage and other power CAN related data. Provides multi-faceted data support for research and battery drive capabilities of electric vehicle batteries. 3.CAN bus and data logger introduction
3.1 CAN bus introduction
CAN is an abbreviation of Controller Area Network (hereinafter referred to as CAN) and is an ISO international standardized serial communication protocol. In addition to the bus topology, the in-vehicle network must have excellent anti-interference ability; extremely strong error detection and processing capability; meet the real-time requirements of information transmission; and have fault diagnosis and processing capabilities. In addition, considering the cost factor, the control interface structure is simple and easy to configure. Based on the above requirements, the high performance, high reliability, real-time and compatibility of the CAN bus and its unique design features are fully in line with the application requirements of the automotive network. Since the introduction of CAN by Bosch in the 1980s, CAN has been standardized by ISO11898 and ISO11519, and is now the standard protocol for European automotive networks.
3.2 Car CAN Data DBC Analysis
Due to the promotion of technology and the increasing demand for driving, the number of CAN nodes in the car is increasing, and the data in the network is getting larger and larger. In order to facilitate the design and maintenance of the whole vehicle, the car CAN data is analyzed and managed by the database, which is the DBC analysis we mentioned. The DBC file is a standard database file. It was originally created by Vector. Later, for the unified management and diagnostic testing of automotive data, most OEMs have a corresponding DBC file database. The process of DBC analysis is to convert the hexadecimal data transmitted by the car CAN network into the physical quantities we are familiar with, such as the speed, speed, temperature and so on. The CAN data acquisition instrument neoVI FIRE provided in this paper is fully supported for data DBC analysis, and the accompanying software Vehicle Spy3 can freely create and modify DBC database files.
3.3 FIRE data acquisition instrument and function software Vehicle SPY3
The neoVI FIRE has a car data logger with 4 CAN channels and 4 LIN channels, allowing users to simultaneously view message data on multiple networks. The neoVI FIRE achieves no-loss monitoring with an accuracy of 10 microseconds, ensuring the integrity of all data acquisition in electric vehicles.
neoVI FIRE supports MicroSD card recording data with a maximum of 64G data capacity. 64G is equivalent to storing 2 billion standard messages and 200 messages in 1s. It can collect more than 110 days of data and can be used without PC. Make data records. The vehicle Spy software is used to configure the neoVI FIRE recorder, including message filtering. After the PC is disconnected from the vehicle, the vehicle network information can be recorded to know that the memory card is full. The versatile design and full industrial temperature range allow the neoVI FIRE to operate in harsh environments with a maximum input voltage of 40V, which fully meets the testing needs of electric vehicles. In addition, there is no need to continuously interact with the PC to avoid the work of people following the car.
The supporting software Vehicle Spy is a tool that integrates functions such as diagnostics, node/ECU simulation, data acquisition, automatic testing and in-vehicle communication network monitoring. Vehicle Spy can implement network monitoring, data decoding, data acquisition/recording, node simulation, and automatic testing.
4. System architecture
The system architecture of the electric vehicle data acquisition scheme in this paper is based on the abbreviated architecture in practical applications. The FIRE data recorder can realize the complete recording of CAN bus data, and collect the target data through filtering and script function. After BDC analysis, it will not only connect. The external parameters (voltage, current, temperature, capacity, etc.) of each battery cell to the CAN bus are recorded and stored, and the actual vehicle CAN data is also recorded into the neoVI FIRE data recorder, after which data of different formats can be exported. The document facilitates further analysis.
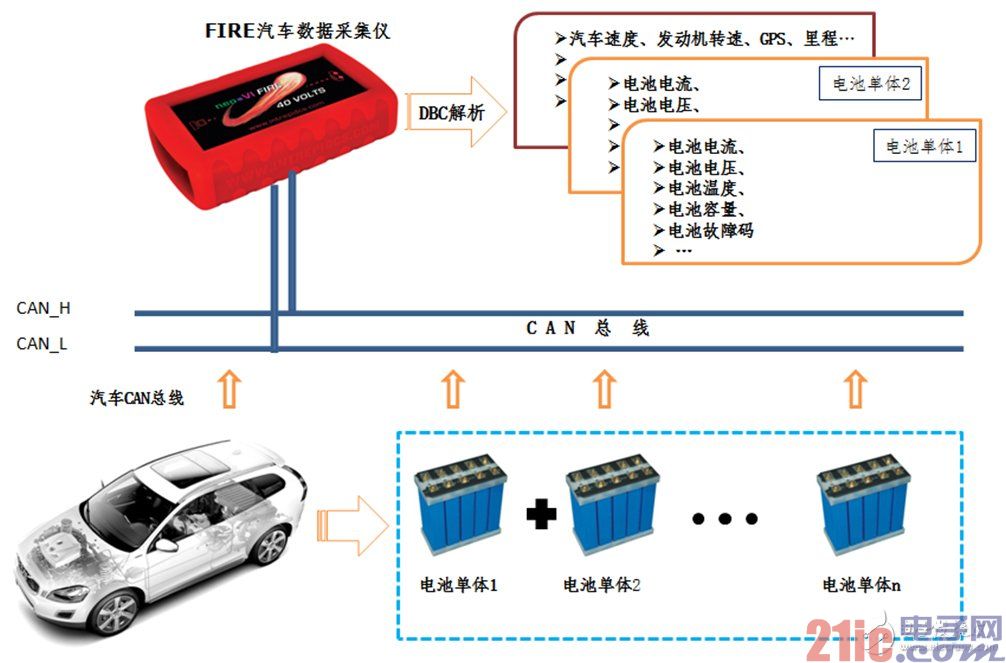
5. Data collection configuration features and operations
5.1 Process configuration
In the hardware neoVI FIRE recorder can quickly configure the corresponding CAN communication baud rate, after the dual-channel CAN bus is connected to the battery pack CAN network and the car power CAN network respectively, the software Vehicle Spy3 software uses the process configuration operation to load the DBC file. Select and filter the acquisition signal, collect the trigger mode configuration, generate the configuration script, and finally download the configuration script to the neoVI FIRE recorder for offline data collection.
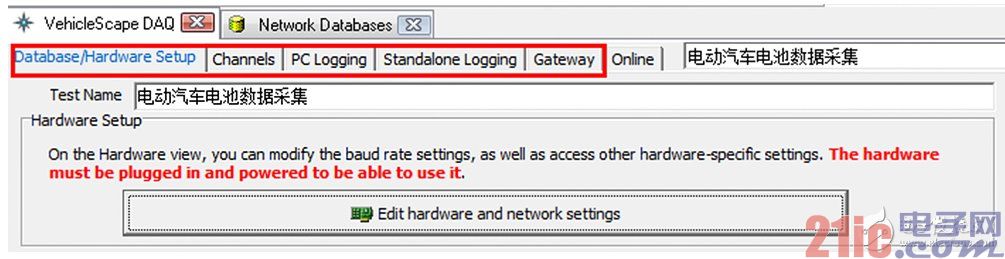
5.2 support to add multiple DBC files
Vehicle Spy3 software can directly open the vehicle data acquisition function (Vehiclescape DAQ) to quickly create the acquisition configuration project, and then add multiple DBC database files:
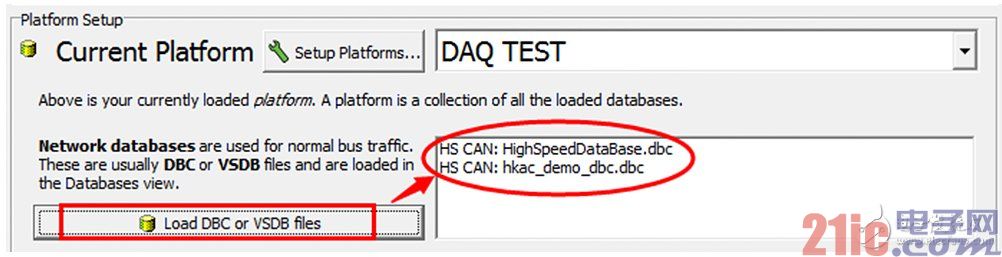
5.3 Filtering the selection signal
After loading the DBC file, the battery-related signal and the vehicle-powered CAN-related signal can be loaded and imported into the record list.
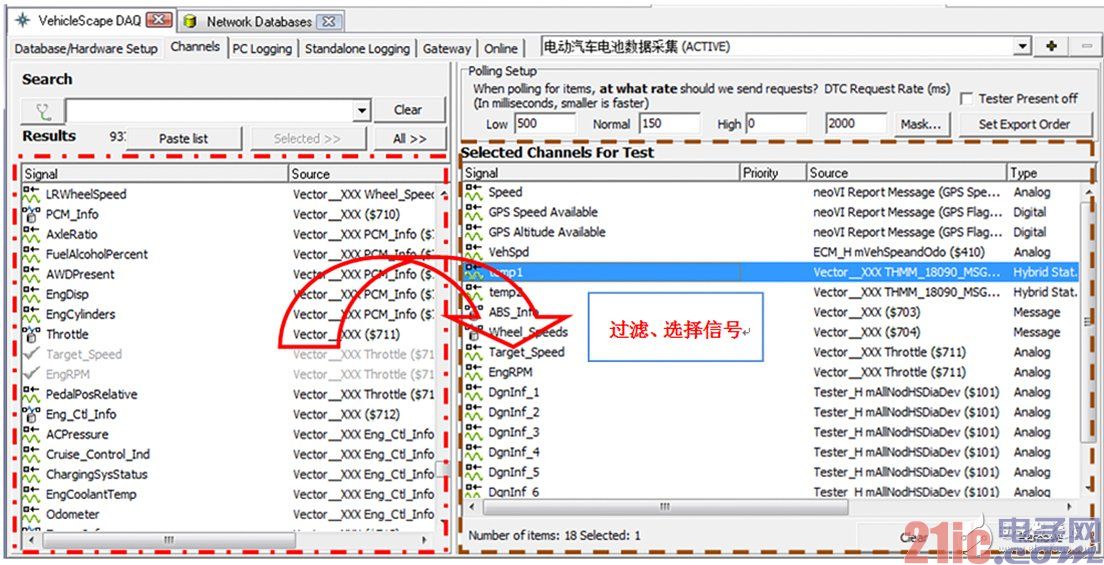
5.4 Acquisition Trigger Configuration
1. Various trigger modes can be selected during data acquisition: immediate trigger, expression trigger and trigger trigger. The expression trigger can set different logical expressions, and can freely implement different trigger requirements.
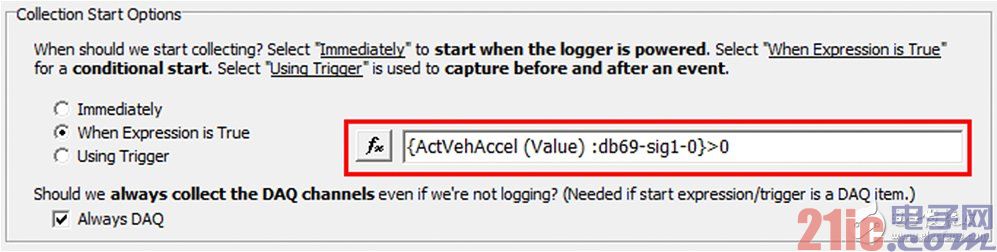
2. Support record end condition setting: You can set the number of recorded messages or end the recording by an expression.

5.5 Recorder Power Support Record Sleep
In order to improve the power utilization of electric vehicles, the neoVI FIRE data logger can be configured with hardware sleep conditions to maximize the power consumption of electric vehicles.
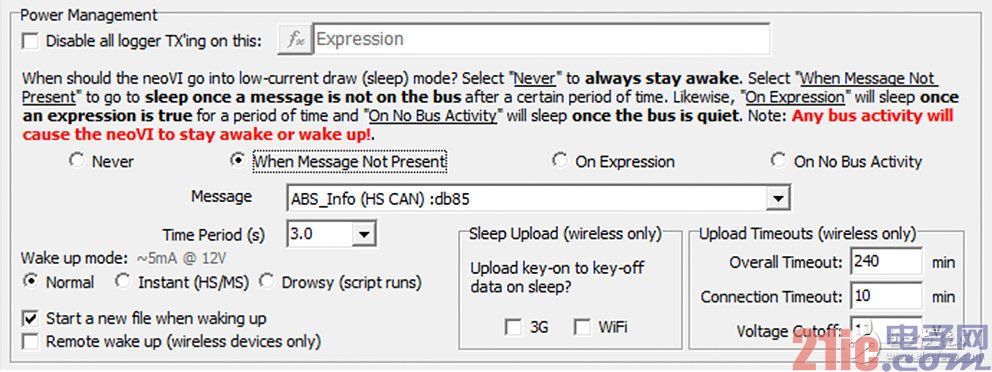
5.6 Export multiple data formats
The Vehicle Spy3 recording configuration can not only export CAN original messages, but also support the export of DBC parsed signal data, such as battery voltage, temperature and other signals. The supported formats are CSV format for most data analysis software, and also support Vector's ASC format. In addition, the exported data file can be set to file size, or file merge and chunked storage. These methods provide powerful data support for studying various aspects of the battery.

Product introduction of Nylon Braided Sleeve For Cable Harness
1.Ideal for Cable and wire protection,insulation,indentification and decoration.
2. Help you control and tidy cable wire harness.
3. Expandable, Made of PA 6.6, Softer than Pet Sleeve.
Product benifits of Nylon Braided Sleeve For Cable Harness
1.PA 6.6 Material, Light Weight & Flexible.
2.ecpandable type,Easy to Install, remove.
even if some with bulky or large connectors.
3.Abrasion Resistant and Flame redardant.
4.Totally expanded the sleeving can reach at least one point five times than the initial dimension.
Item |
Nylon Expandable Braided Sleeve for cable wire harness |
Material |
Polyamide 6.6 |
Operating range |
-60C to +160C |
Melt point |
256C +/- 10C |
Flammability |
VW-1 |
Certificate |
ROHS |
Standard color |
Black and gray |
Cutting tool |
Hot knife |
Nylon Braided Sleeve
Nylon Cable Sleeve,Nylon Braided Sleeves,Nylon Expandable Braided Sleeves,Pet Braided Cable Sleeving
Shenzhen Huiyunhai Tech.Co.,Ltd , https://www.hyhbraidedsleeve.com